From Log to Bowl:
A Step by Step Journey
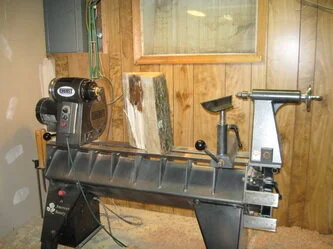

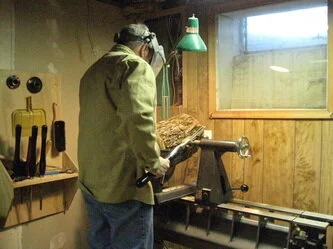
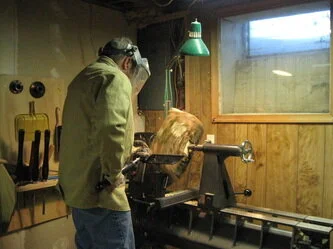
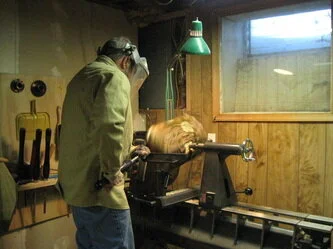
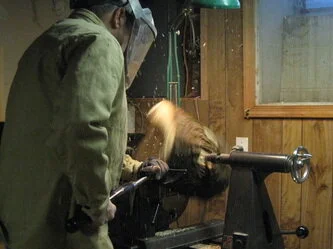
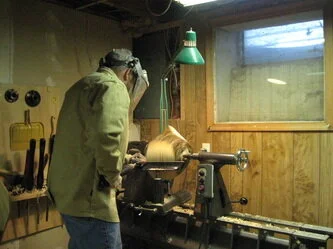

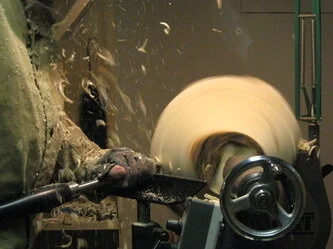


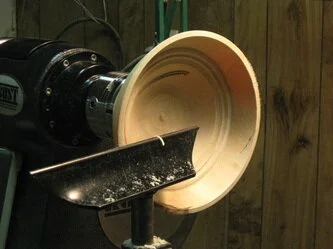

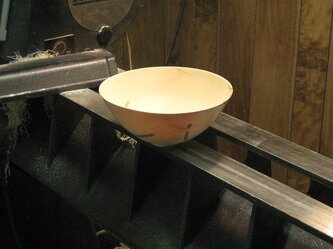
A Bowl is Born!
I like to work with wood that has not yet dried. While the wood is heavier to mount on the lathe, the facts that it cuts more easily and has less dust outweigh that issue. The wood I use from trees that have been cut down for various reasons but not specifically for turning purposes. Also, the wood I use for bowls, vessels, and vases is from trees indigenous to North America and occasionally, Hawaii. The only time I use what is referred to as exotic wood is for accent such as finals where the tighter grain and wood hardness is needed to make the piece at all.
The photos show how a bowl is turned from a half log. Most of the cutting and shaping of the wood is done with a gouge that has an edge profile compatible with cutting the wood efficiently. To remove the wood from the interior of a vase or vessel, it is necessary to use tools that scrape the wood to cut it as the gouge cannot maintain contact with the wood due to the angles necessary to do the cutting. With bowls that curve inward to form the rim but are mostly open, I use the gouge to remove most of the wood then go to the scrapers to complete the interior profile. Before the piece is removed from the lathe it is sanded up to 600 grit and the base is shaped.
As you may have noted in looking at the pieces in the Gallery, the walls of my bowls are fairly thin. I turn a vast majority of my work to between 3/16" to 1/4" thick. There are times when to bowl may be thinner or slightly thicker than that but that is my usual thickness range.I feel the pieces look more elegant with the thinner walls and they are lighter to handle. There are times where the piece is large enough that the thinner walls just wouldn't look right so I will go thicker.
Once the piece is turned, it must be dried before any finish is applied. I simply set the pieces aside in a pa[er or plastic bag in a dry room and track to the reduction of moisture in the wood. It is necessary to turn the piece over so it dries evenly and therefore not crack during the drying. This works most of the time because "wood is wood" and it will do what it wants regardless. it is during this drying process that the pieces will change shape, sometimes going visibly oval or warping the rims.
Finishing the pieces is a somewhat protracted process. I finish all my work with 4 coats of finish using various types of finish depending on the design and intended use of the piece. The bowls receive the first application on the outside and once that is dry, the inside receives its coat of finish. With both sides dry the entire bowl is then sanded with 400 grit and the process is repeated until all 4 coats are applied. The final sanding is done with 4000 grit-that is not a typo-and some pieces are buffed but not all. At that point, the piece is done.